-
Book Overview & Buying
-
Table Of Contents
-
Feedback & Rating
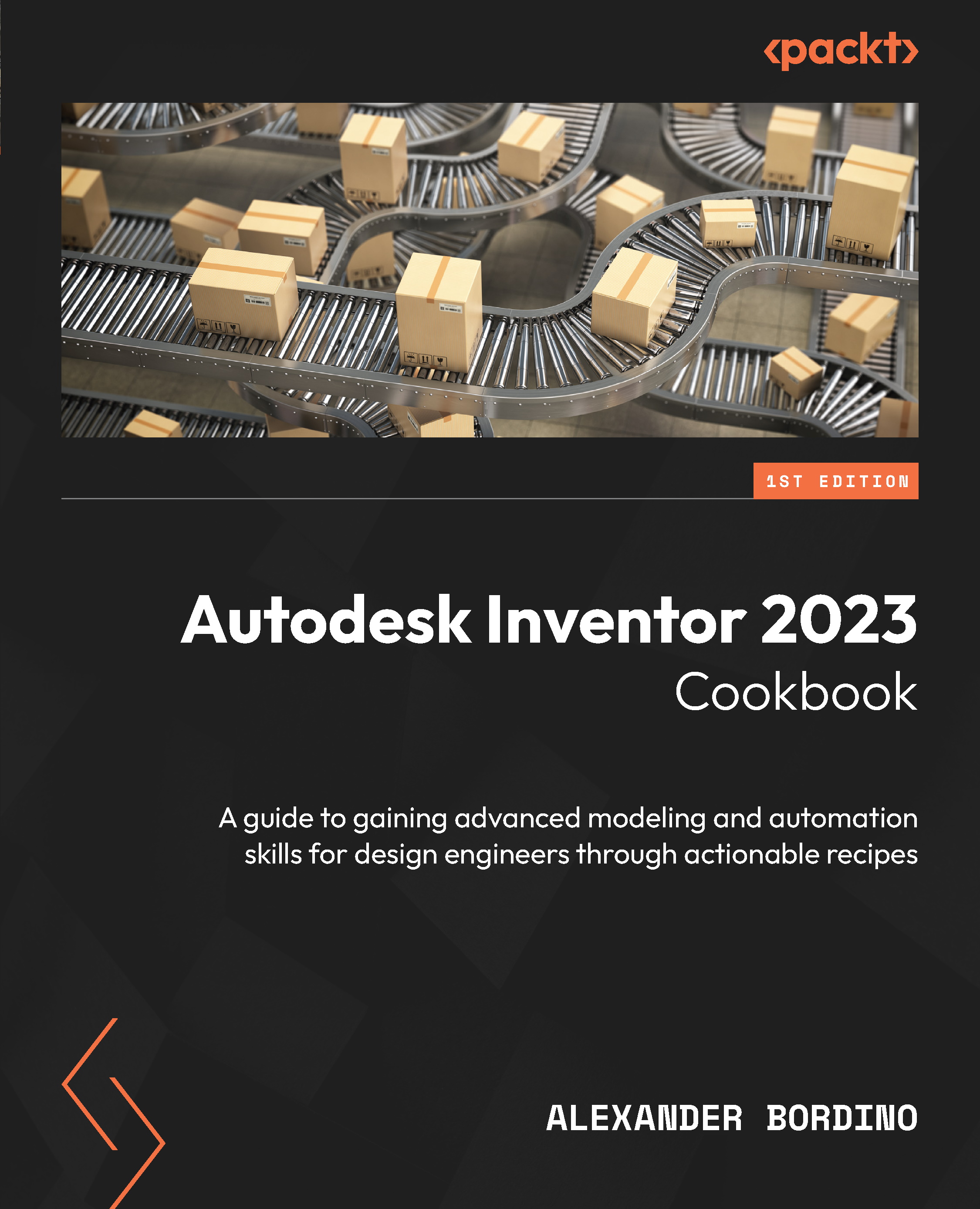
Autodesk Inventor 2023 Cookbook
By :
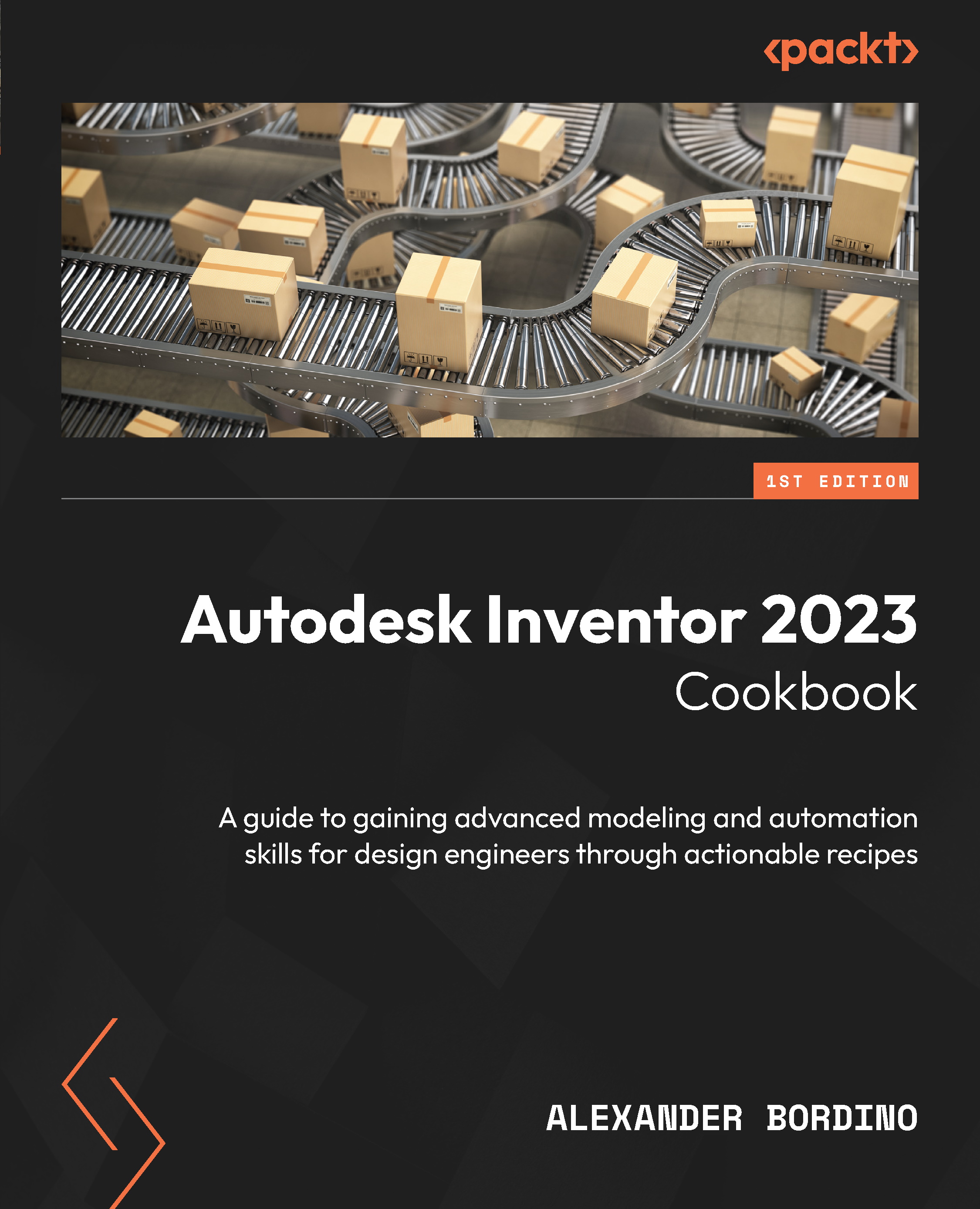
In this recipe, you will create a small subassembly of parts to complete the design of a mountain bike shock absorber. You will learn how to create multiple bodies, in a model, and add features to the bodies. The completed assembly is shown in Figure 2.5, which includes the subcomponent that you will design using the multi-body design process. The rest of the components are supplied as separate solids.
Figure 2.5 shows the completed assembly of the shock absorber containing the part we will create:
Figure 2.5: Full assembly of the shock absorber part we will create
Start to familiarize yourself with Figure 2.5 as it contains the part we will make (dimensions are not given yet but will be given to you in stages throughout this recipe).
The files that you need for this recipe can be found in the Chapter 2
folder of the Inventor 2023
Cookbook
folder.
You can also open Shock_Absorber_Assy.iam
as a reference, which can be found in the Chapter 2
folder too (although it is not needed directly for the recipe).
To begin the recipe, we will need to create the first component within the assembly:
Standard Metric (mm) .ipt
template. To do this, select File | New | Metric. Choose Standard (mm) .ipt
for the template, then click Create to complete.18 mm
diameter circle that is centered on the origin, as shown here in Figure 2.6:Figure 2.6: The start of the initial sketch
Next, create the rest of the sketch geometry, as shown in Figure 2.7. To do this, draw a construction line from the origin of the circle downward by 21 mm
. Next, from the end point, create a horizontal 9 mm
line from the construction line end point, then a 3 mm
vertical line from the end point of the previous line. This is shown in Figure 2.7:
Figure 2.7: The next sketch lines to apply
Ensure the sketch is fully defined before progressing to step 4.
3 mm
in length and snap to the edge of the circle. Set the radius of the arc to 15 mm
. To fully constrain this arc, you will then need to add a tangent constraint between the arc and the circle, as shown in Figure 2.8:Figure 2.8: 15 mm three-point arc created with a tangency relationship applied between the arc and circle
Figure 2.9: The sketch with the mirror applied
14 mm
for Distance A. Then, ensure Direction is set to Symmetric, then select OK.In this case, with 14 mm
set as the overall extrude length, this extends the extrusion both ways by 7 mm
in each direction.
Figure 2.10: Extrusion of the profile applied at 14 mm from the center in both directions
Figure 2.11: The sketch geometry required to create the next features of the part
5 mm
.Figure 2.12: The two extrusions created in the same operation
Using the XY plane, in the 3D Model tab, select Mirror and mirror the protruding extrusion from the Model Browser. This replicates the extrusion we created previously, but on the other side of the part.
Figure 2.13: Mirror operation in action showing the plane and copied feature geometry
10 mm
diameter circle central to the base of the model. Once complete, select Finish Sketch and then extrude the circle by 50 mm
, in the direction away from the model. This is shown in Figure 2.14:Figure 2.14: 10 mm circle extruded by 50 mm from the base of the part
The first solid body is now complete with additional features added. In the Model Browser, you will see the Solid Bodies folder now shows (1). The additional solids will now be created within the part file.
Figure 2.15: Solid Bodies folder of the Model Browser expanded, showing one solid body in the part file
18 mm
in diameter.Figure 2.16: Sketch of the circle that must be created, 18 mm in diameter
Crucially, at this stage, open the Output area of the Extrude menu and set Boolean as New Solid. This will create the feature as a separate and independent solid from Solid1. Select OK to complete this.
A second solid has now been created.
Figure 2.17: Creation of the new solid using the Extrusion command
.5 mm
fillet to the edge of Solid2, as shown here in Figure 2.18. Select OK to close the command.Figure 2.18: .5mm fillet added to the new Solid2 edge
A second instance of Solid2 is required on the other side of Solid1; rather than creating or modeling this again, we can mirror Solid2 along the XY plane to create a second identical instance of Solid2.
Figure 2.19: Mirror command dialog box showing the settings that need to be applied to mirror Solid2
1 mm
hole that goes through all three solids created. Create a new sketch on the face of Solid2, as shown in Figure 2.20. Add a sketch point where the arrow is shown and then exit the sketch.Figure 2.20: Sketch to be created on Solid2 with an arrow indicating the location of the sketch point
1 mm
diameter. In the Solids area, select all three solids to enable the hole to pass through all three independent solids created. This shows how you can perform feature edits in multi-body design, on multiple solids at once if required. Select OK to complete the hole.Figure 2.21: Hole command with settings applied in step 19, showing hole going through all three independent solids
Part1.ipt
in the Shock Absorber
folder, within the Chapter
2
folder.Figure 2.22: Make Components dialog box with the options required
Select Solid 1 and change the name to SA_MALE_1.ipt
. Repeat this for the two other solids, as shown in Figure 2.23, with sequential numbers, in the Component Name column.
Then, select the Page button above the Template column. Navigate to the Metric tab and select the Standard (mm) .ipt
template to use. Then, click OK.
Figure 2.23: Make Components: Bodies dialog box with component names changed and templates redefined
.ipt
files. To review the results, click OPEN and navigate back to the Inventor 2023 Cookbook
folder, where the solid parts will be located. This is shown in Figure 2.24:Figure 2.24: Newly created separate .ipt part files from the solids initially created
In this recipe, you have successfully created three independent solids as part of a multi-body design workflow to create a subassembly of parts for a shock absorber. You have then exported each solid as a separate part file. The parent multi-body part file is associative with the exported independent parts, which means that if we change the parent part, the child (exported) parts also change.
Change the font size
Change margin width
Change background colour