-
Book Overview & Buying
-
Table Of Contents
-
Feedback & Rating
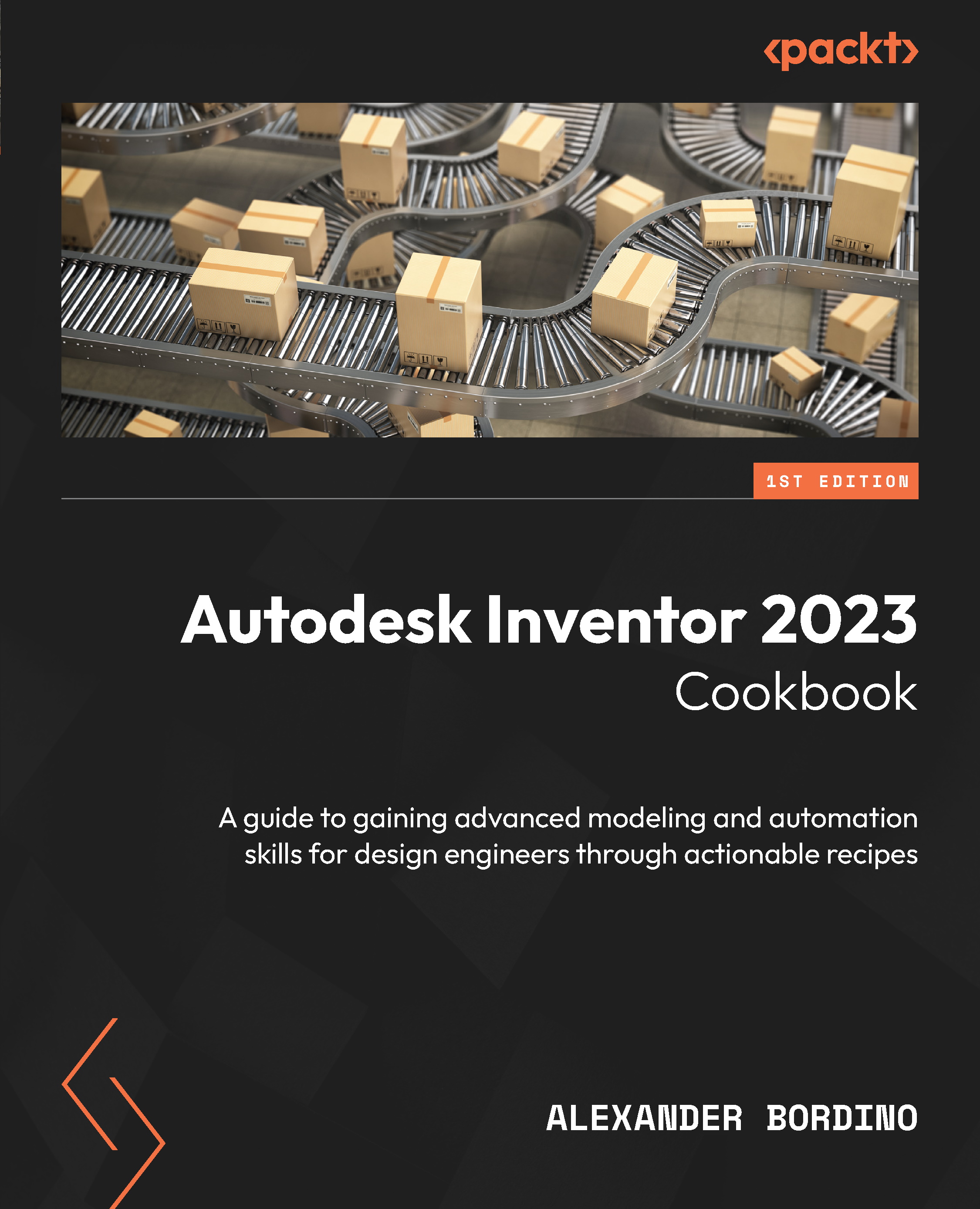
Autodesk Inventor 2023 Cookbook
By :
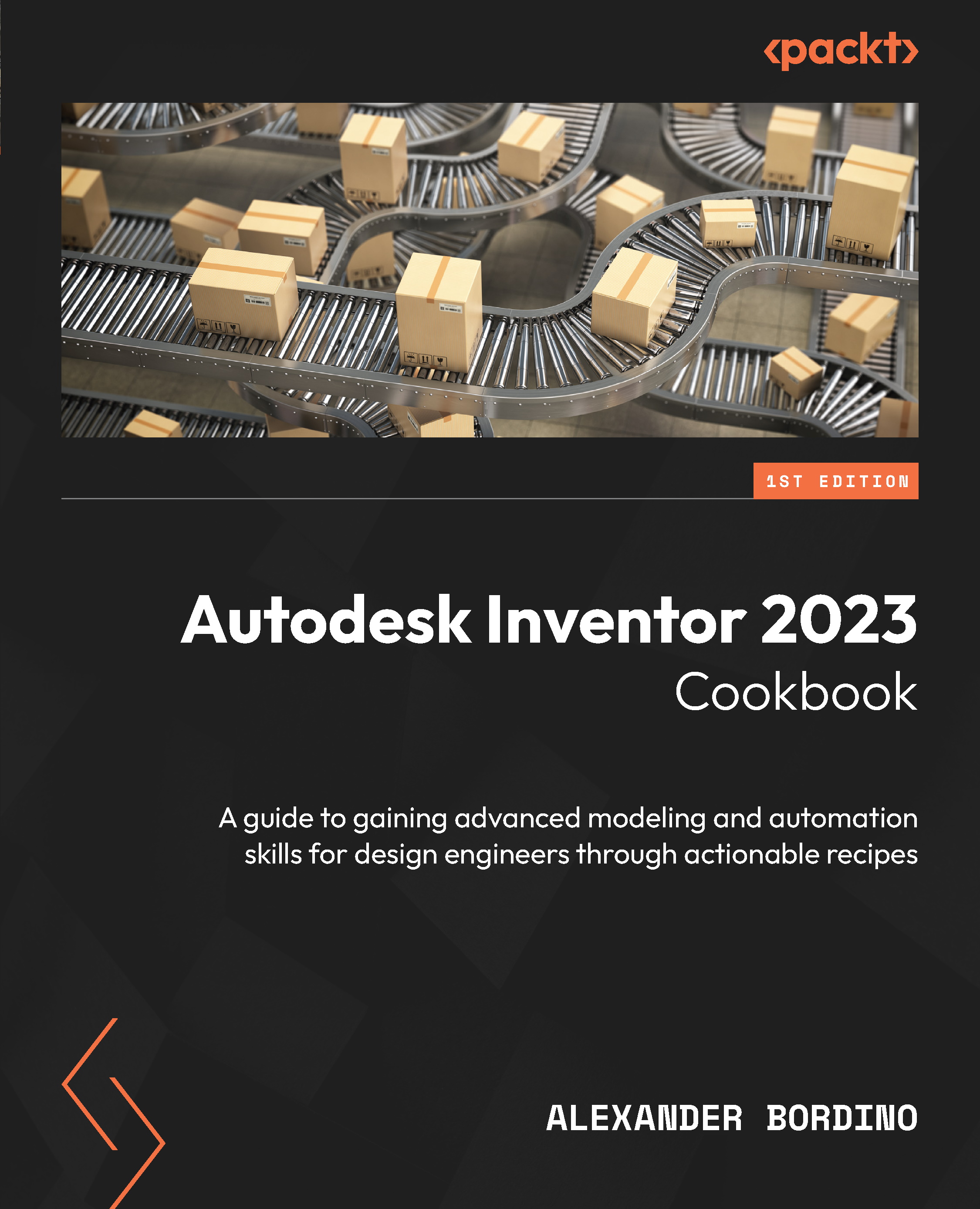
Within Inventor, there is a variety of modeling methodologies that can be used and combined. In this section, we will examine each type and how they can be used.
The bottom-up design process is the traditional way of modeling and creating an assembly within a CAD environment. It is a part-centric process, whereby each part’s geometry is created separately in its own independent .ipt
part file and then combined into a single top-level assembly .iam
file. Independent parts are combined with Mates constraints in the final assembly to create the desired outcome of the final top-level assembly.
The advantages of this methodology are that each part has its own independent file, and therefore its own file structure, which is much easier to understand and organize. Parts can also be updated and changed without influencing related parts in the referenced assembly.
The disadvantages of this structure are that the level of rework can be much higher. Because part files are not linked through geometry, when part A changes in an assembly, the other parts that it may interact with, such as part B or C, will not automatically update. This means that the designer now must spend time manually updating and correcting parts B and C in the assembly to ensure the desired interface and fit between these components is achieved. Depending on the level of change and complexity of the design, this can take a significant amount of time.
Problems can also arise when separate part files are first combined into the assembly. Often, this is due to a lack of engineering information communication, with problems such as misalignment, interference, or an incomplete design.
In Figure 2.1, you can see an example of the structure of a bottom-up design methodology:
Figure 2.1: Diagram of bottom-up design
The multi-body design methodology places critical design information within a top-level assembly and communicates this information to lower levels of the product structure.
Multi-body design begins with the creation of a single part or solid as a reference model. Additional solids are then created inside the same part file and exported as parts into an assembly environment. Any changes to this methodology, to the original part, are reflected in the linked parts and assembly, resulting in a true parametric methodology.
The advantages of multi-body design are that all the design resides in a single .ipt
file, with the solid bodies extracted later to create parts and an assembly. The reliance on Mates and onstraints in the assembly environment is reduced as parts are created in place and on location.
With this method, there is usually less reworking required as the parametric link between solids from the initial part file is maintained, so as design changes are made, the linked solids also update to reflect the changes, resulting in less rework.
Finally, the body’s visibility can be controlled as a group instead of at an individual feature level, and relationships between bodies can be created and broken freely.
In Figure 2.2, you can see an example of the multi-body design methodology:
Figure 2.2: Diagram of multi-body design
Layout design involves taking an existing arrangement or drawing from a 2D format such as .dwg
, importing it into an Inventor sketch environment, and then combining with sketch relationships and feature modeling techniques to derive 3D components from a 2D layout.
The 2D sketch initially contains all the design intent, dimensions, and spatial locations of components within the assembly. Each component is usually broken down into a sketch block, which can be achieved in both Inventor and AutoCAD.
This is widely used in some companies if there is a reliance on the initial design being completed as a 2D layout first, prior to 3D models. It can also be used with other techniques, such as bottom-up or multi-body. An example would be if a supplier of a component could only supply a 2D drawing file, yet the designer required a 3D model to place in the top-level assembly; a 3D variant could be created from the 2D drawing as a reference using the layout design methodology.
With layout design, if the original 2D sketch is updated, these changes are reflected in the 3D model. This means the design can be manipulated from the 2D imported sketch, including the movement and interaction of components.
Figure 2.3 shows the layout design methodology:
Figure 2.3: Diagram of the layout design process
Adaptive modeling design uses references from an existing assembly to create parts inside an assembly file, from the projection of existing geometry. Adaptive links are made in this process between sketches and features so that if the parent updates, the child sketch or feature also updates. With an adaptive part, it is intrinsically linked to other parts it shares an adaptive link with.
The advantage of adaptivity is that this link can also be broken if required. It is ideal for determining very specific tolerances in place and on location of where the end part will reside. Because of the adaptive link, the level of rework or updates is further reduced. As parts are created from the assembly environment, the number of mates and constraints needed to position the end components is reduced.
Figure 2.4 shows the adaptive modeling design methodology:
Figure 2.4: Diagram of the adaptive design process
In the next part of the chapter, we will apply this knowledge within Inventor and work with each design methodology.
Change the font size
Change margin width
Change background colour