-
Book Overview & Buying
-
Table Of Contents
-
Feedback & Rating
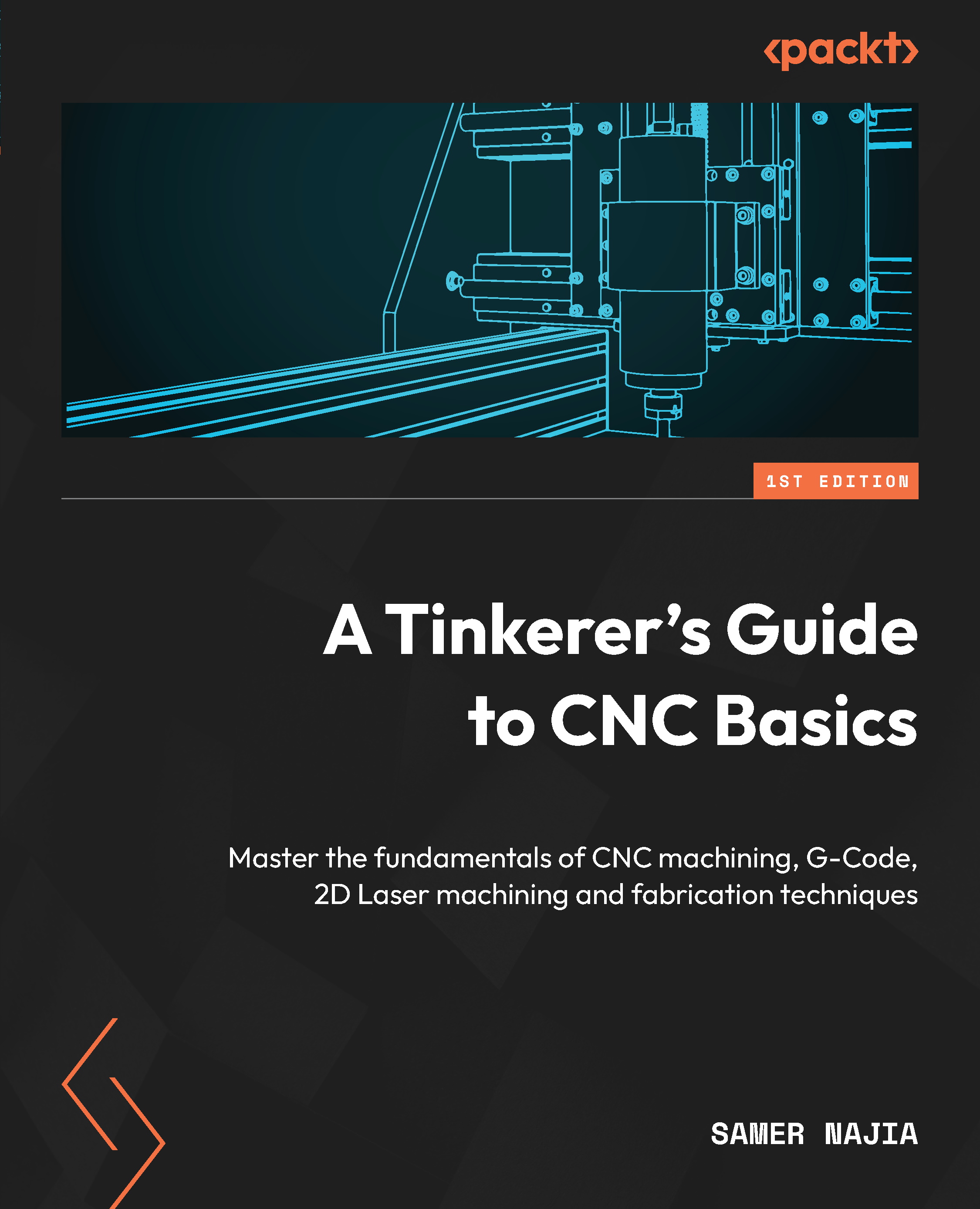
A Tinkerer's Guide to CNC Basics
By :
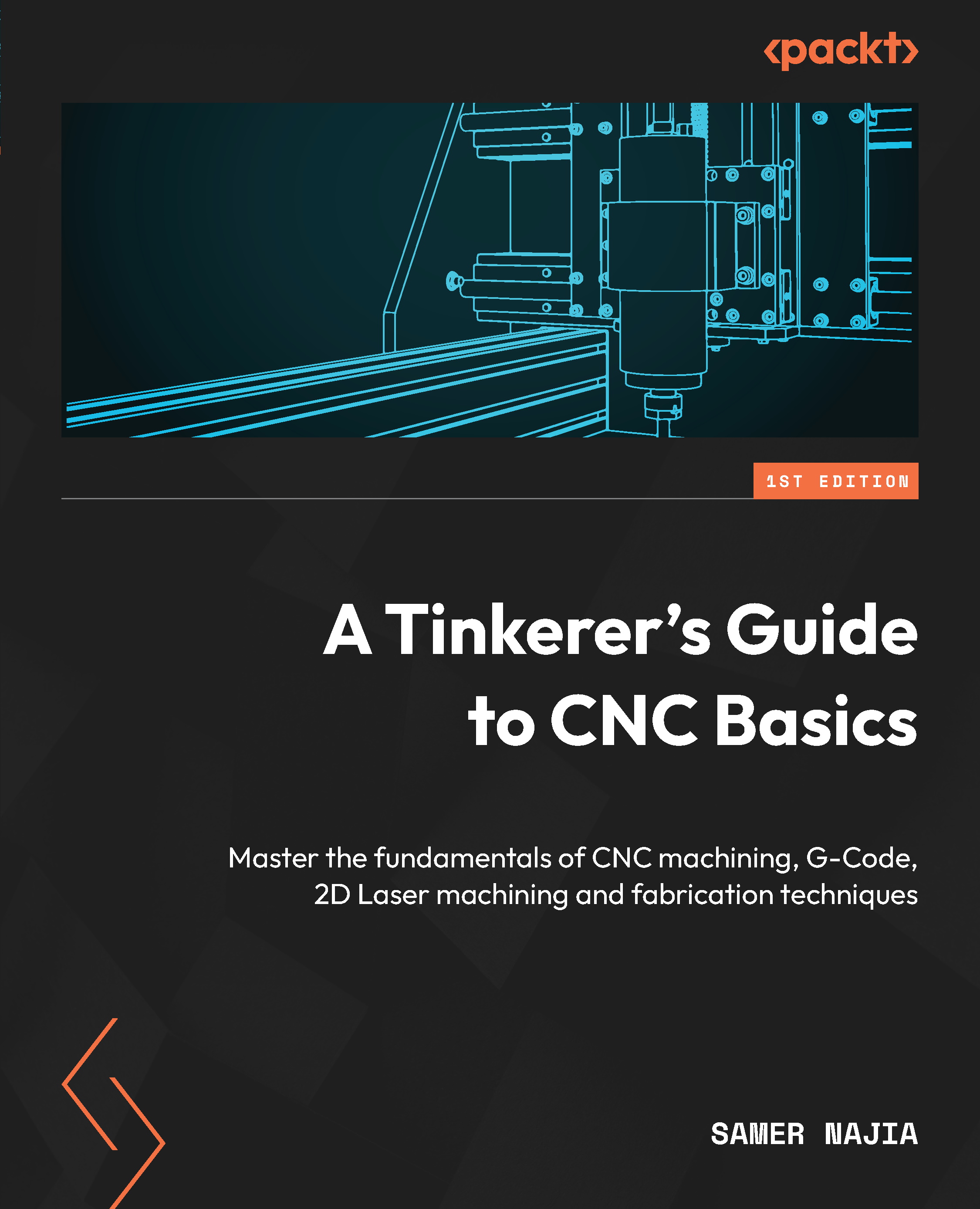
For our purposes, I am using 3 mm plywood to cut out my bulkhead because most of the balsa wood in my shop is smaller planks for park-flyer-type (i.e., smaller scale) airplanes. I use the same plywood for model rocket fins, and while light and easy to mill and machine, it is very durable.
Both balsa and plywood are going to chip on the “bottom” surface (the surface facing the wasteboard) if we are not careful with what endmill we use. To prevent the “tearing out” that would happen with plywood, I recommend a flat-head downcut endmill. I am using a single-flute flat-nosed endmill with a 1/8” shank. These are commonly available from various vendors, and you should take into account that you will likely break a few as a matter of course. I like to keep my feed rate slow, at or below 1000 mm/s for thicker plywood and 2000 mm/s or less for thicker material. For the spindle, keep it below 24,000 RPM.
...Change the font size
Change margin width
Change background colour